

Surfaces left-bare should be heavily chromated. Does plating make that big a difference knowing that it's going to be painted also? Mark HollenbeckĪ. Also, I found out that the casting is painted after plating. Our plater said that he would be willing to go thicker on the clear. Can anyone give me some direction on how to get the customer to accept going to clear. He is asking for more info on the difference between ASTM B633 Our plater would like to go to a clear zinc, but our customer is under the assumption that the clear will not do as good a job with corrosion resistance and salt spray life.
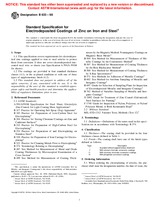
We are getting poor coverage on the as-cast surface of some steel castings using a yellow Zinc chromate. Additional types have been added to permit non-chromate passivate treatments to be used in replacement of hexavalent chromium.Q. It is the responsibility of the user of this standard to establish appropriate safety and health practices and determine the applicability of regulatory limitations prior to use.ġ.4 This standard has been revised to address RoHS requirements that seek to limit the exposure of workers and the public from exposure to toxic metals. This standard does not purport to address all of the safety concerns, if any, associated with its use. It does not cover electrodeposited zinc-coated steel wire or sheets (see Specification A 591/A 591M for sheets).ġ.2 The coatings are provided in four standard thickness classes (4.1), in the as-plated condition or with one of three types of supplementary finish (4.2).ġ.3 High strength metals, unless otherwise specified, including high strength steels having a tensile strength greater than 1700 MPa (247 ksi R c 46) shall not be electroplated. 1.1 This specification covers requirements for electrodeposited zinc coatings applied to iron or steel articles to protect them from corrosion.
